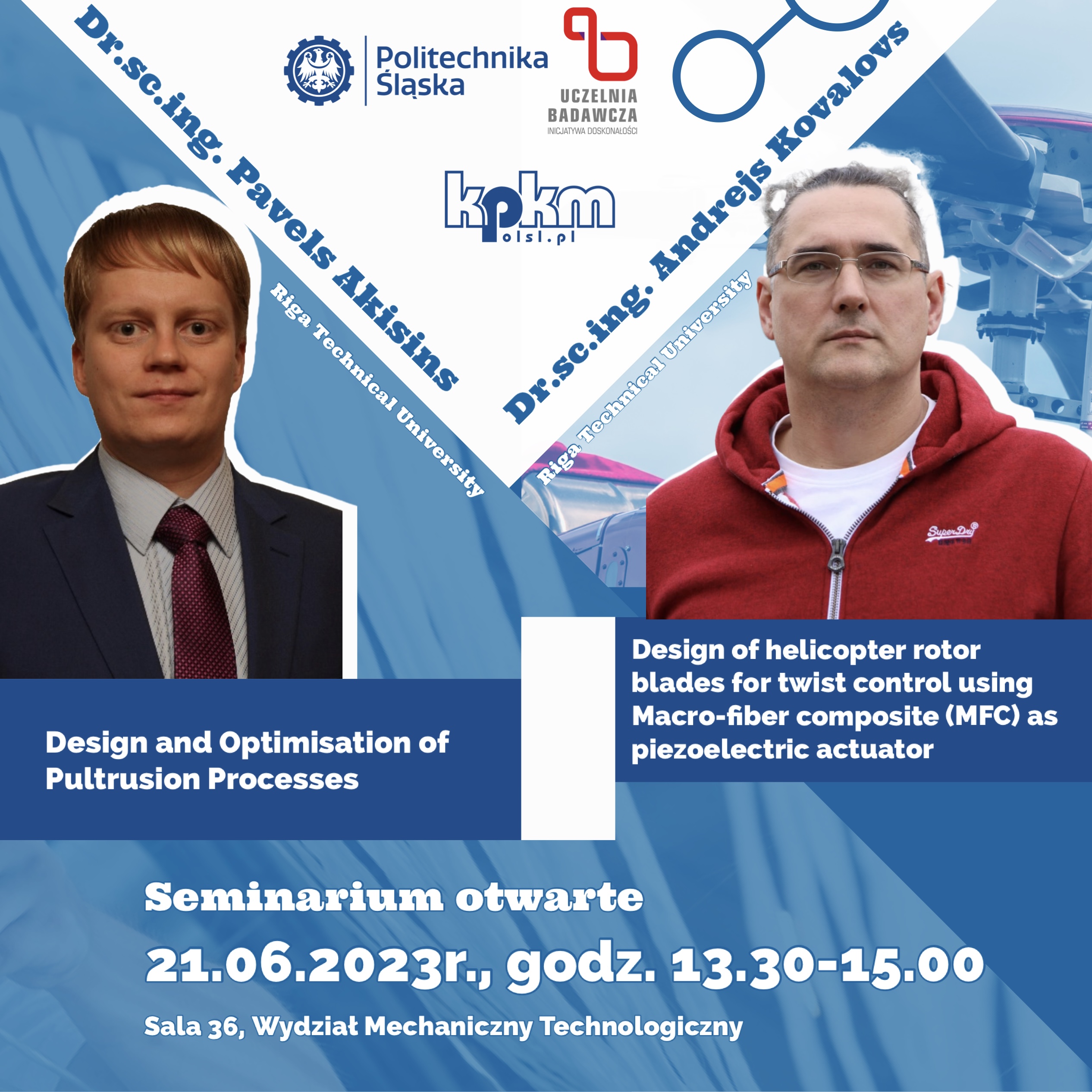
Dr Kovalovs i Dr Akisins opowiedzą o swoich doświadczeniach z kompozytami
Dnia 2️⃣1️⃣ .0️⃣6️⃣.2️⃣0️⃣2️⃣3️⃣ o godzinie 1️⃣3️⃣.3️⃣0️⃣ na seminarium naukowym Katedra Podstaw Konstrukcji Maszyn, Politechnika Śląska w ramach cyklu "Mechanika i diagnostyka konstrukcji" będziemy gościć 👨🏼🎓dwóch wybitnych naukowców z University of Riga z ciekawymi referatami związanymi z tematyką kompozytów:
Design and Optimisation of Pultrusion Processes
Design of helicopter rotor blades for twist control using Macro-fiber composite (MFC) as piezoelectric actuator
Seminarium odbędzie się w sali 3️⃣6️⃣ na Wydziale Mechanicznym Technologicznym Politechniki Śląskiej.
👉 Seminarium będzie również transmitowane on-line:
https://polsl-pl.zoom.us/j/94274600844?pwd=VjRFM1VyWEd2SGFmckxFVEx3S0I4QT09
Poniżej krótkie noty biograficzne naszych gości oraz streszczenia referatów:
Dr.sc.ing. Andrejs Kovalovs is a researcher at the Department of Composite Materials and Structures of the Riga Technical University since 2006. He received PhD in mechanical engineering at the Riga Technical University in 2015. His main research interests are design and optimization of composite structures. He has authored 51 scientific publications abstracted in the Scopus database (h index =9). He has participated in the implementation of national and international projects under EU FP programmes.
Design of helicopter rotor blades for twist control using Macro-fiber composite (MFC) as piezoelectric actuator
In flight, helicopter rotor blades produce significant vibrations and noise as a result of aerodynamic loads acting on highly flexible rotating blades, which leads to the discomfort of passengers, increases pilot workload, reduces the fatigue life of structural elements, limits the forward flight speed, and increases maintenance costs. With the emergence of piezoelectric materials, an Active Twist Rotor concept was proposed. Actuators integrated into the rotor blade skin generate dynamic blade twists and cambers adapted to flight conditions at any given time, which significantly reduces vibrations and noise and improves the flight performance. The objective of the present study is to develop a methodology, based on the planning of experiments and response surface technique, for the optimum design of active rotor blades using piezoelectric actuators to obtain high piezoelectric actuation forces and twist displacements at a minimum actuator weight and energy applied.
Dr.sc.ing. Pavels Akisins is a researcher at the Department of Composite Materials and Structures of the Riga Technical University since 2013. He received PhD in mechanical engineering at the Riga Technical University in 2018. His main research interests are design and optimization of composite structures and their manufacturing processes. He has authored 28 scientific publications abstracted in the Scopus database (h index =9). He has participated in the implementation of national and international projects under EU FP and H2020 programmes. Pavels Akisins is an expert at the Latvian Council of Science.
Design and Optimisation of Pultrusion Processes
Pultrusion is a continuous and cost-effective process for a production of fibre-reinforced polymer (FRF) composite structural components with a constant cross-sectional profile.
A considerable cost reduction of the pultrusion products can be reached by an improvement of the effectiveness of pultrusion processes. This could be done by: (1) optimisation of conventional pultrusion processes and (2) an application of new effective heating sources instead of electrical heaters.
To obtain low cost and high quality pultruded profiles, an optimisation methodology based on the planning of experiments and response surface technique was developed. Using non-direct optimisation methodology, the working maps allowing to obtain minimal cost solutions in dependence on processing parameters and surrounding temperature were developed.
A high frequency electromagnetic energy source characterized by the fast, instantaneous, non-contact and volumetric heating was examined as the best choice for the pultrusion applications. To develop advanced microwave assisted pultrusion processes new simulation methodology consisting of two sub-models: electromagnetic and thermo-chemical was developed.
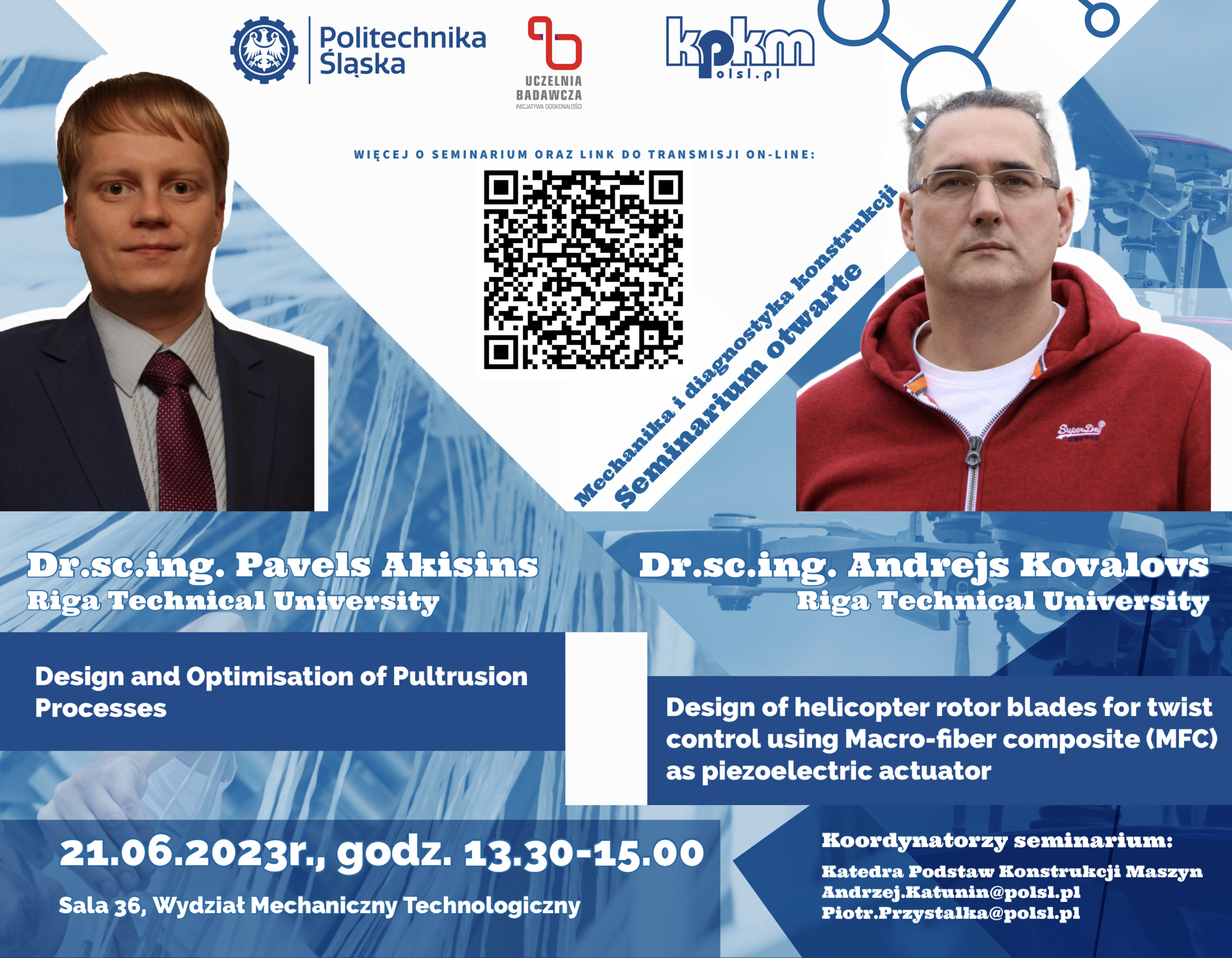