13 marca 2024 o godz. 11:00 odbyła się obrona pracy doktorskiej mgra inż. Tomasza Zadorożnego, pt.: „Minimalizacja odkształceń cieplnych w wyniku inteligentnej optymalizacji rozmieszczenia punktów mocowań w obszarze komponentu spawanego”.
Promotorem rozprawy był dr hab. inż. Mirosław Szczepanik prof. PŚ, natomiast recenzentami dr hab. inż. Leszek Łatka prof PWr z Politechniki Wrocławskiej, dr hab. inż. Dariusz Fydrych prof PG z Politechniki Gdańskiej oraz dr hab. inż. Andrzej Kubit prof. PRz z Politechniki Rzeszowskiej. Komisja Doktorska uchwaliła wnioski do Rady Dyscypliny Inżynieria Mechaniczna o nadanie mgr inż. Tomaszowi Zadorożnemu stopnia doktora nauk technicznych w dyscyplinie Inżynieria Mechaniczna.
Optymalizacja procesów technologicznych z powodu wielu czynników mających wpływ na ich przebieg jest wyjątkowo trudna oraz czasochłonna. Prawidłowo przeprowadzona symulacja procesu wraz z jego optymalizacją pozwala usprawnić etap produkcji przyczyniając się do znacznej redukcji kosztów związanych z czasem technologicznym oraz potencjalnymi naprawami. W niniejszej pracy przedstawiono opis problemu dotyczącego trwałych odkształceń termicznych po procesie spawania. Omówiono różnego rodzaju wady oraz metody ich naprawy wskazując na wyraźną potrzebę ich ograniczenia, które przekłada się na stabilizację procesu produkcyjnego oraz poprawę jakości produktu. W dalszej części dokonano opisu opracowanego systemu służącego do symulacji procesu spawania oraz optymalizacji rozmieszczenia punktów mocowań w obszarze komponentu spawanego w celu minimalizacji odkształceń cieplnych. Do realizacji postawionego zadania użyto komercyjnego oprogramowania HyperWorks, który został połączony z autorskimi algorytmami wspomagającymi proces tworzenia modelu numerycznego oraz optymalizacji. W pracy przedstawiono również przykład dla stosunkowo prostej konstrukcji, dla której szczegółowo opisano schemat postępowania oraz działania podczas prowadzenia symulacji procesu i optymalizacji. Dodatkowo w celu walidacji opracowanego systemu przeprowadzono złożoną symulację numeryczną procesu spawania poszycia pojazdu kolejowego oraz optymalizację doboru punktów podparcia. Analiza dokładnie odwzorowywała rzeczywiste warunki oraz parametry jakie są używane podczas procesu produkcyjnego. Uwzględniono również poszczególne etapy produkcji oraz sekwencje spawania poszczególnych komponentów. Otrzymane wyniki porównano z pomiarami rzeczywistymi konstrukcji po zakończonym procesie co pozwoliło potwierdzić słuszność przyjętych założeń podczas tworzenia omawianego systemu. Zaprezentowany system optymalizacji oraz podejście do problemu wskazuję, iż na wstępnym etapie projektowania konstrukcji oraz planowania procesu produkcyjnego możliwy jest odpowiedni dobór rozmieszczenia punktów mocowań tak aby ograniczyć odkształcenia cieplne. Omówione rozwiązanie zostało z powodzeniem wdrożone w przedsiębiorstwie.
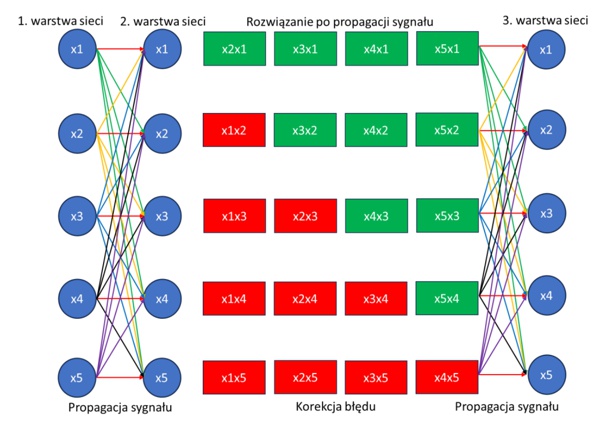
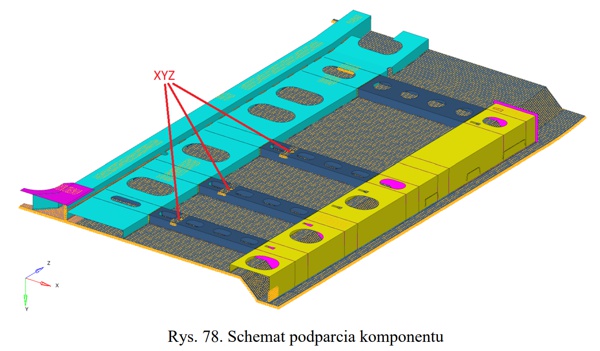