Opracowanie technologii formowania anodowych powłok tlenkowych na stopach metali lekkich na drodze plazmowej obróbki elektrolitycznej w kierunku otrzymywania kompleksowych systemów zabezpieczenia powierzchni
Opracowanie technologii formowania anodowych powłok tlenkowych na stopach metali lekkich na drodze plazmowej obróbki elektrolitycznej w kierunku otrzymywania kompleksowych systemów zabezpieczenia powierzchni
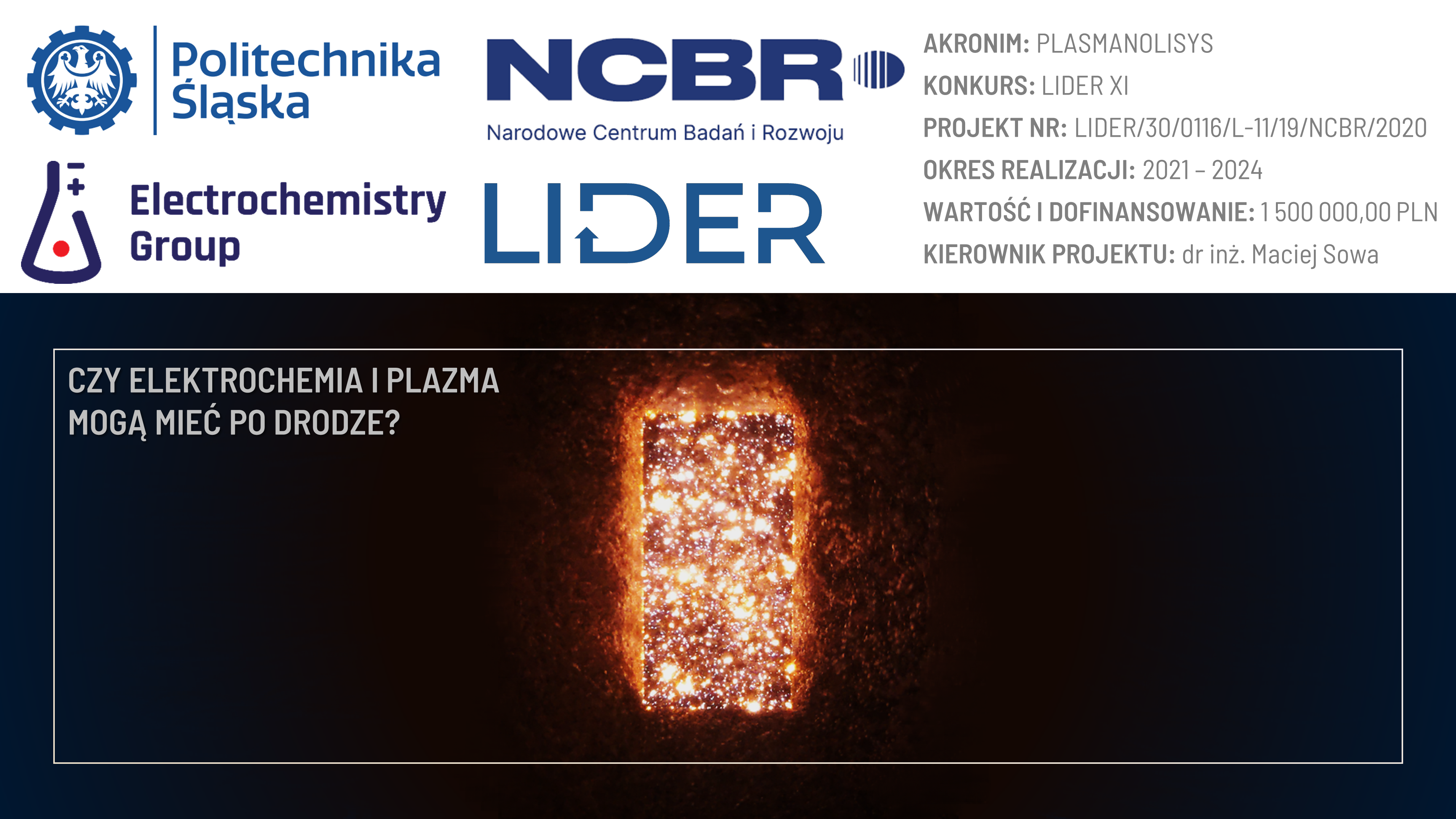
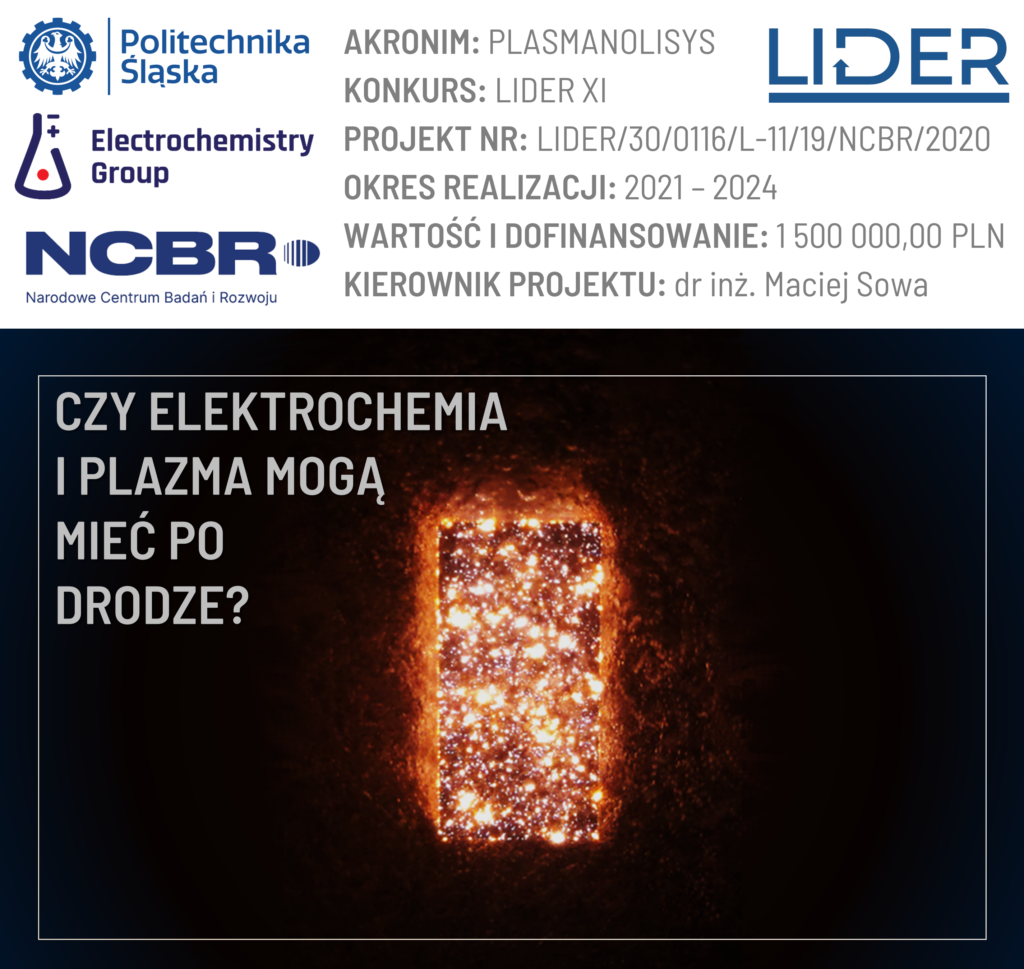
Plazmowa obróbka "na zimno"
Zważywszy na stale postępujące w czasie zmiany klimatyczne na Ziemi oraz rosnącą trudność w pozyskiwaniu paliw kopalnych, jasnym staje się, że współczesne społeczeństwa w coraz większym stopniu poszukują nowoczesnych technologii przyjaznych dla środowiska. Takie rozwiązania obejmują np. obniżenie emisji gazów cieplarnianych do atmosfery, poprzez redukcję zużycia energii, przy równoczesnym przyczynieniu się do poprawy jakości życia. Przykładem technologii pozwalającej na zrealizowanie wyżej opisanych działań, jest plazmowe utlenianie elektrolityczne (PEO ang. Plasma Electrolytic Oxidation). Proces ten stanowi alternatywę dla powszechnie stosowanego w praktyce anodowania.
Metoda PEO pozwala na formowanie grubych, ceramicznych warstw tlenkowych, które w znaczący sposób poprawiają właściwości mechaniczne (m.in. twardość) oraz odporność korozyjną stopów metali lekkich. Dzięki zabezpieczeniu za pomocą procesu PEO możliwe będzie ich szersze zastosowanie, co może wpłynąć na rozwój lekkich konstrukcji w budownictwie i transporcie, w efekcie zmniejszając koszty paliwa i emisję spalin.
Należy jednak mieć na uwadze, że proces PEO to technologia wciąż dość młoda. W ramach projektu opracowywana jest technologia wytwarzania warstw tlenkowych na stopach aluminium i magnezu, która będzie konkurencyjna lub uzupełniająca względem anodowania konwencjonalnego. Podjęte zostaną działania mające na celu:
Określenie wpływu warunków obróbki PEO na cechy strukturalne i funkcjonalne uzyskanych w procesie anodowych powłok tlenkowych
Wykazanie efektu dodatkowej obróbki wstępnej na jakość formowanych w wyniku PEO warstw
Zbadanie możliwości nadania dodatkowej funkcjonalności warstw poprzez obróbkę wykańczającą

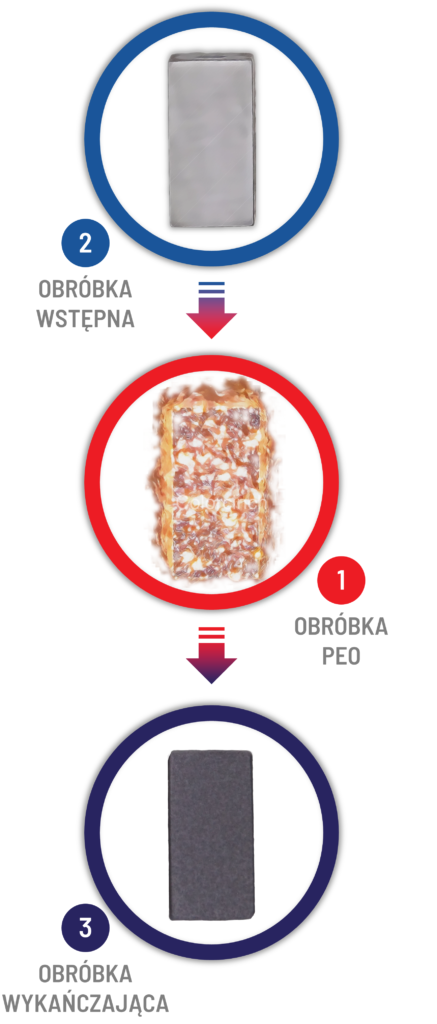
Ujarzmianie plazmy
Cechą szczególną technologii PEO jest występowanie drobnych, krótkotrwałych iskier (lub mikro-wyładowań), powstałych na skutek działania na obrabiany detal prądem elektrycznym o wysokim napięciu elektrolizy (350-600 V). Przy zachowaniu odpowiedniego reżimu procesowego możliwym jest ukierunkowanie zjawisk plazmowych do stanu "iskrzenia miękkiego".

Iskrzenie miękkie uzyskiwane na stopach aluminium niesie ze sobą wiele korzyści. Przede wszystkim napięcie potrzebne do jego podtrzymania jest zwykle o 30-40% niższe niż w przypadku klasycznego procesu PEO (obniżenie zużycia energii). Poza tym formowana w ten sposób powłoka jest wzbogacana w niezwykle twardy i odporny na zużycie ścierne minerał - korund (wł. odmiana alfa tlenku glinu). Faza ta jest umiejscowiona w tzw. warstwie zwartej powłoki PEO. Im prędzej dochodzi do zmiękczenia plazmy, tym mniejsze nakłady energii są potrzebne do wytworzenia powłoki. Dlatego w projekcie zbadano wpływ obróbki wstępnej na przebieg procesu PEO, co stanowi jego część 2. Oprócz tego odporność korozyjna powłok uzyskiwanych w wariancie procesu ze zmiękczoną plazmą ulega pewnemu pogorszeniu. Stąd potrzeba dalszej modyfikacji, czego dotyczy część 3. realizacji projektu.

Kontrola od początku do końca
Powstawanie plazmy na powierzchni jest warunkowane obecnością warstwy zaporowej o konkretnych właściwościach izolacyjnych. Poprzez odpowiednio zaprojektowaną obróbkę wstępną można stworzyć podłoże, które wpływa nie tylko na przebieg procesu PEO (czas, zużycie energii elektrycznej), ale również na odporność korozyjną oferowanej przez otrzymaną warstwę tlenkową. W projekcie opracowano metody obróbki wstępnej oparte o warstwy konwersyjne i metody anodowania konwencjonalnego.
Najbardziej wierzchnia część tlenku otrzymanego w procesie PEO stanowi warstwę porowatą. Charakteryzuje się ona stosunkowo niskimi właściwościami mechanicznymi, z powodu obecności porów. Te jednak mogą służyć do załadunku substancji, które umożliwiają dalszą modyfikację pokryć. Stosując opracowaną w projekcie obróbkę wykańczającą można nie tylko wprowadzić do warstw tlenkowych inhibitory korozji, ale również barwniki organiczne o szerokiej gamie kolorystycznej, co wpływa również na efekt dekoracyjny finalnego wyrobu.
Technologia PEO z wprowadzonymi innowacjami projektowymi w porównaniu do anodowania konwencjonalnego
Metoda PEO wywodzi się od anodowania konwencjonalnego, gdzie detale są zanurzane w roztworach kwasów (np. siarkowego, chromowego; 20-40%), następnie włączane w obwód elektryczny jako anody, podczas gdy katody zanurzone w tej samej kąpieli są wykonane najczęściej ze stali nierdzewnej. Przez obwód przepuszczany jest prąd elektryczny, co powoduje wzrost tlenku na powierzchni detali (na ogół od 20 do 50 μm grubości). Przed samym anodowaniem wymagane jest staranne, wieloetapowe przygotowanie powierzchni (m.in. obróbka mechaniczna, odtłuszczanie, trawienie, dekapowanie, płukanie), a po procesie warstwy uszczelnia się we wrzącej wodzie demineralizowanej.
W technologii plazmowego utleniania elektrolitycznego stosuje się rozcieńczone (maks. 5%), ekologiczne roztwory o pH zasadowym (brak problemu korozji aparatury), a po wstępnym obrobieniu mechanicznym, detale należy wyłącznie odtłuścić. Poza tym układ do elektrolizy nie różni się od anodowania konwencjonalnego poza źródłem zasilania (prostownikiem). Proces wymaga stosunkowo wysokiego napięcia (400-600 V) i prądu (5-25 A/dm^2) i często prowadzony jest w trybie impulsowym i bipolarnym (okresowo zmieniane bieguny napięcia).
Wyższe koszty obróbki PEO w porównaniu do anodowania konwencjonalnego rekompensowane są znacznie wyższymi parametrami technologicznymi, takimi jak twardość, przyczepność, odporność na ścieranie, odporność na korozję.
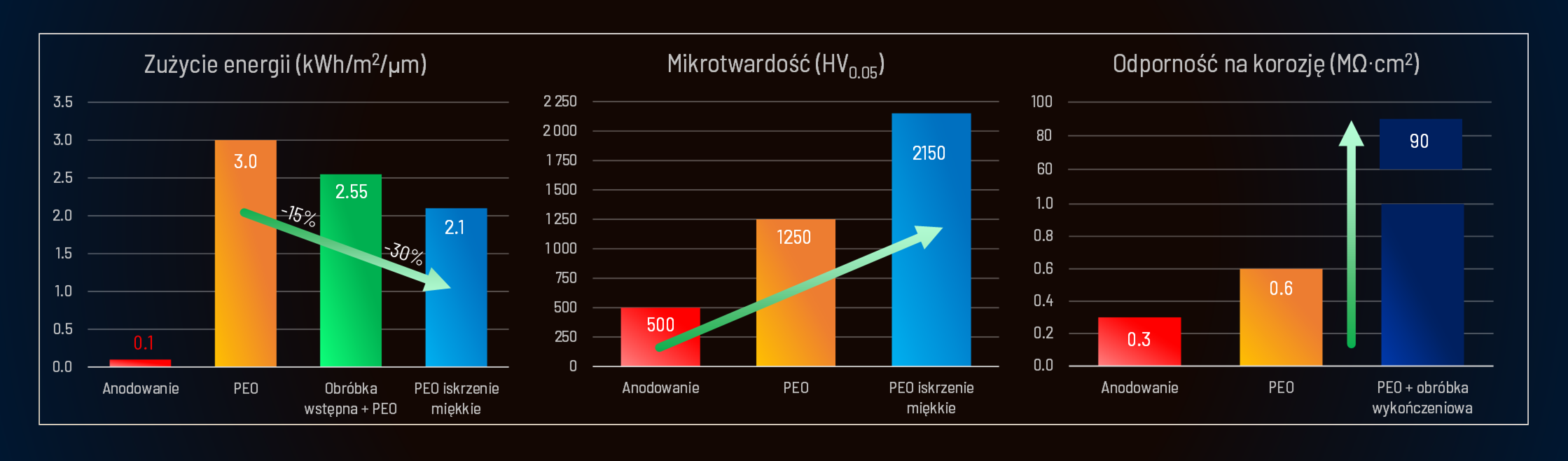
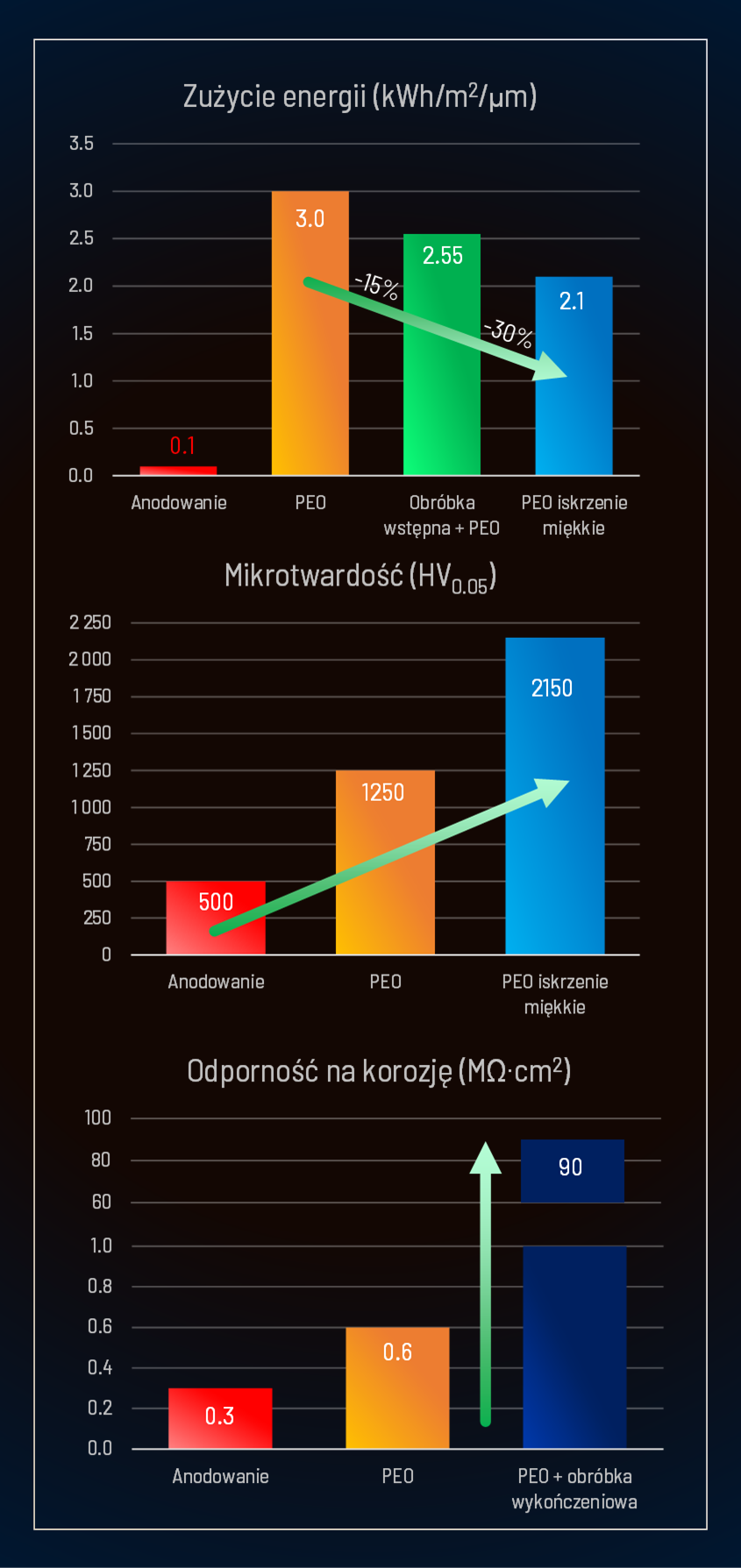
Przykładowe etapy obróbki powierzchni
Pokaż wszystkieZastosowanie
W opracowanej technologii pokrywa się elementy wykonane ze stopów metali lekkich (stopów aluminium, stopów magnezu). Rozwiązanie ma zastosowanie wszędzie tam, gdzie wymagane są równocześnie: niska masa konstrukcji oraz odporność powierzchni na zużycie mechaniczne i korozyjne. Poza tym jako technologia bezchromowa, metoda jest zgodna zaleceniami unijnymi wg RoHS oraz REACH.
Sport:
Ramy rowerowe, kije golfowe, bloki silnikowe, elementy wymagające tribologicznie (silniki stosowane w motorsporcie); lekkie konstrukcje magnezowe stosuje się również w nowoczesnych wózkach inwalidzkich
Przemysł kosmiczny:
Przeciwdziałanie spawaniu na zimno (ang. cold welding, contact welding) elementów stykających się w przestrzeni kosmicznej (np. drzwi, śluzy etc.), osłony termiczne, łożyska kriogeniczne
Przemysł lotniczy:
Obudowa przekładni śmigłowców, elementy silników odrzutowych
Przemysł samochodowy:
Układ hamulcowy (dyski hamulcowe - zamiast ciężkich elementów z żeliwa), warstwa w parze tribologicznej tłok/cylinder, pierścienie uszczelniające, podkładki mocujące, rolki
Inne:
Budowa pomp turbomolekularnych (rotory o skomplikowanej geometrii); przemysł chemiczny (elementy maszynerii podatne na działanie chemikaliów - np. wyścielenie pomp); przemysł zbrojeniowy (sprzęt osobisty żołnierzy, obudowy urządzeń elektronicznych)
Nasze filmy popularnonaukowe o technologii PEO na YouTube
Źródła zewnętrzne

Artykuł naukowy (Open Access)
M.Sowa et al. Corrosion Inhibitor-Modified Plasma Electrolytic Oxidation Coatings on 6061 Aluminum Alloy, Materials 14 (2021) 619

Artykuł naukowy (Open Access)
M.Sowa et al. Electrochemical characterization of anti-corrosion coatings formed on 6061 aluminum alloy by plasma electrolytic oxidation in the corrosion inhibitor-enriched aqueous solutions, Electrochim. Acta 424 (2022) 140652

Doniesienie prasowe dotyczące wyników projektu
V. Case, Understanding PEO Coatings, Product Finishing