Cooperation
Computer simulations
We have over 25 years of experience in computer numerical simulations using commercial CAE systems. These systems are based on finite element method in the form of MSC.Software (MSC.Patran/Nastran, MSC.Mentat/Marc) and Ansys Multiphysics.
In addition, our own software is used for numerical simulations using finite element method, boundary element method and finite difference method. We carry out works concerning, among others:
- linear statics,
- natural vibration,
- nonlinear analysis (geometrical and material nonlinearities, including time),
- contact buckling analysis,
- modal analysis and forced vibration as a function of frequency,
- modal analysis and forced vibrations as a function of time,
- dynamic calculations for random excitations
- structural optimization and sensitivity analysis
- thermal analyses – linear and nonlinear (calculations of radiation, conductivity, forced and free convection, non-stationary heat flow),
- fatigue strength and crack propagation analyses,
- thermo-elastic strength analysis and
other coupled issues – including, among others, piezoelectric, electro-thermo-mechanical, acoustic-mechanical coupling - analyses of solidification and crystallization processes
- thermal analyses in transient states,
- real-time virtual simulations, kinematic and dynamic analyses of objects in motion
- design and optimization of structures using classical optimization algorithms
- design and optimization of systems using global optimization algorithms such as genetic algorithms, evolutionary algorithms, artificial immune systems, swarm algorithms
- creation of substitute models of real technical systems – metamodels
Example of numerical simulations
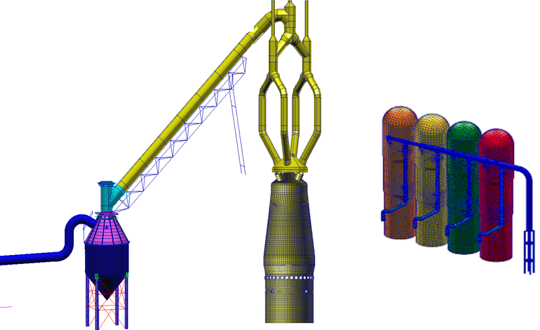
(1994) Strength analyses of the blast furnace process line
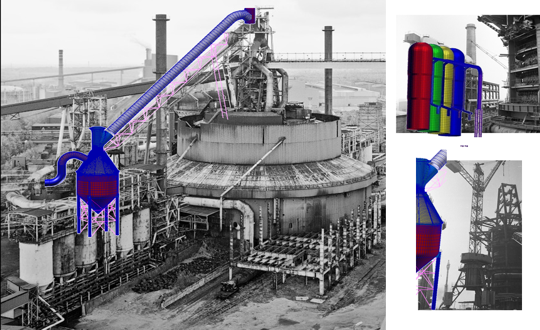
(1994) Strength analyses of the blast furnace process line
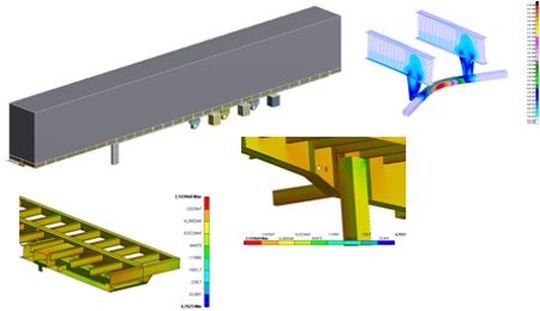
Strength analysis of a semi-trailer truck
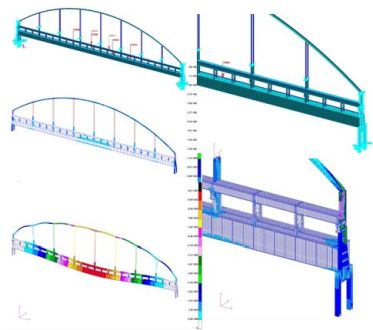
Bridge span strength analysis
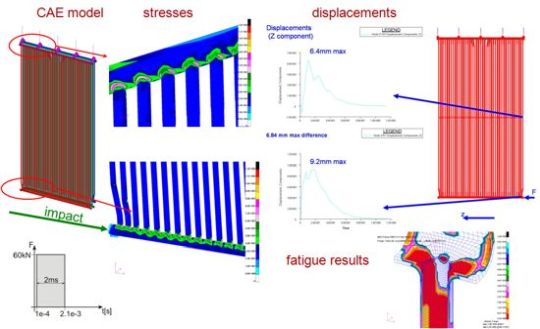
Complex numerical simulation: economizer harp, welded pipe joints (thermoelasticity, dynamics, material and geometric nonlinearities, fatigue)
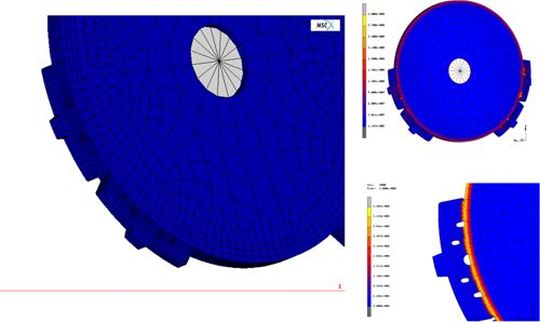
Thermo-mechanical simulation of a disc-brake pad system
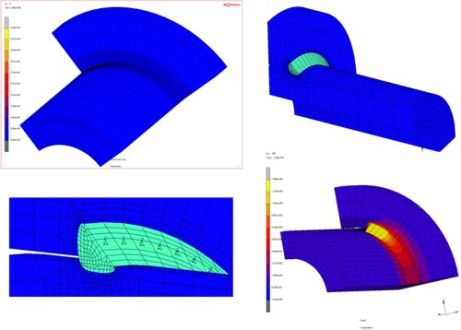
Welding process simulation
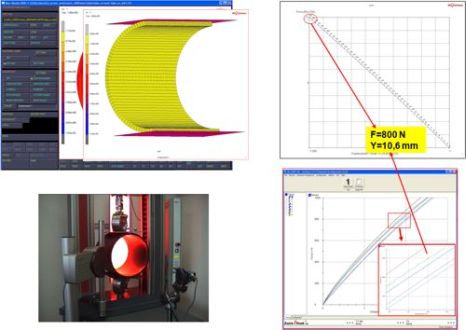
Nonlinear analysis, contact, nonlinear elastic material
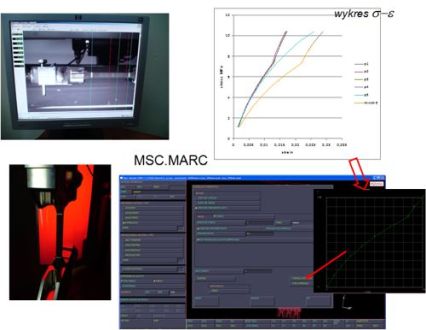
Numerical simulation of stiffness determination for circumferential tube
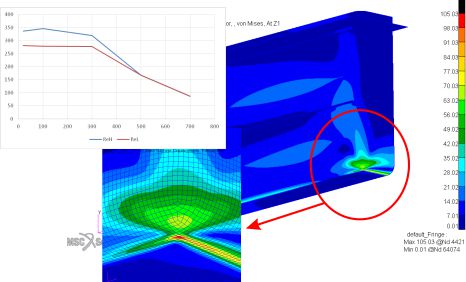
Thermomechanical analysis of the zinc bath
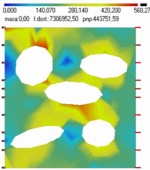
Simulation of remodeling using evolutionary algorithms
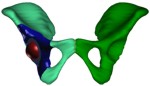
Strength analysis of pelvic bone with implant
Experimental strength testing of materials and structural components:
The Department provides experimental research on such topics as determination of mechanical parameters of materials, fatigue analysis, and verification of numerical models.
We offer research and the possibility of carrying out scientific and research work in the field of:
- Static Tensile Testing of Metals with Determination of Maximum Force
- Static tensile testing of metals with Young’s modulus (using extensometer)
- Testing of axially loaded components
- Testing of components loaded in two axes
- Dynamic tests with sinusoidal excitation in force or displacement control
- Dynamic testing with Whoeler curve
- Dynamic tests with external voltage-controlled excitation
- Low-frequency tests with voltage output sensors
- Strain gauge testing at low frequencies
- Vibration analysis with single and triaxial sensors
- Determination of natural frequencies of vibrations
- Investigation of dynamic properties of engineering materials at ambient temperature (metal, polymer, etc.)
- Testing of vibrations of devices with difficult access (e.g. block transformers),
- Diagnostics of high voltage line insulators (low frequency vibrations),
- Vibration measurements of machine elements resonance frequency
- Vibration measurements of low-speed rotating machines
- Diagnostics of machine drives using direct measurements of shaft vibration velocity.
Tests are carried out using high-end testing machines and modern measuring equipment.
Equipment of laboratories
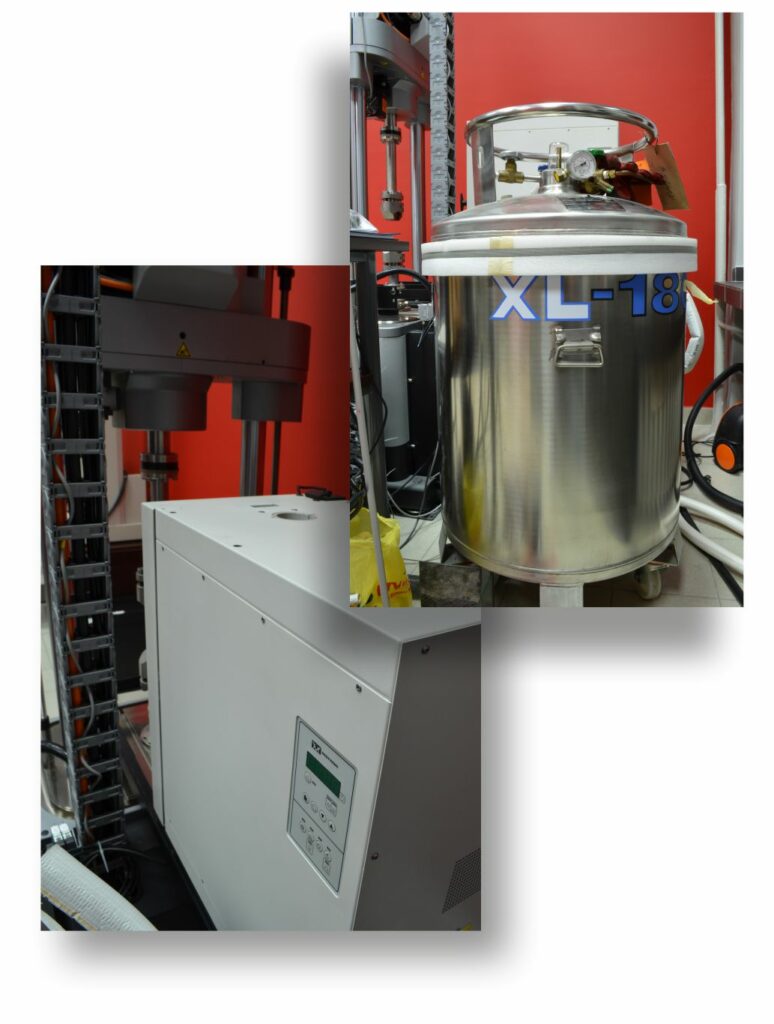
Thermal test chamber (-70 to +350 degrees °C)
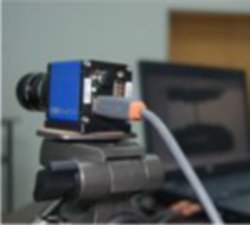
CCD cameras with 1280x1024 dot resolution
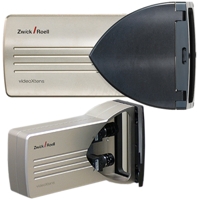
Extensometer video from Zwick Roell
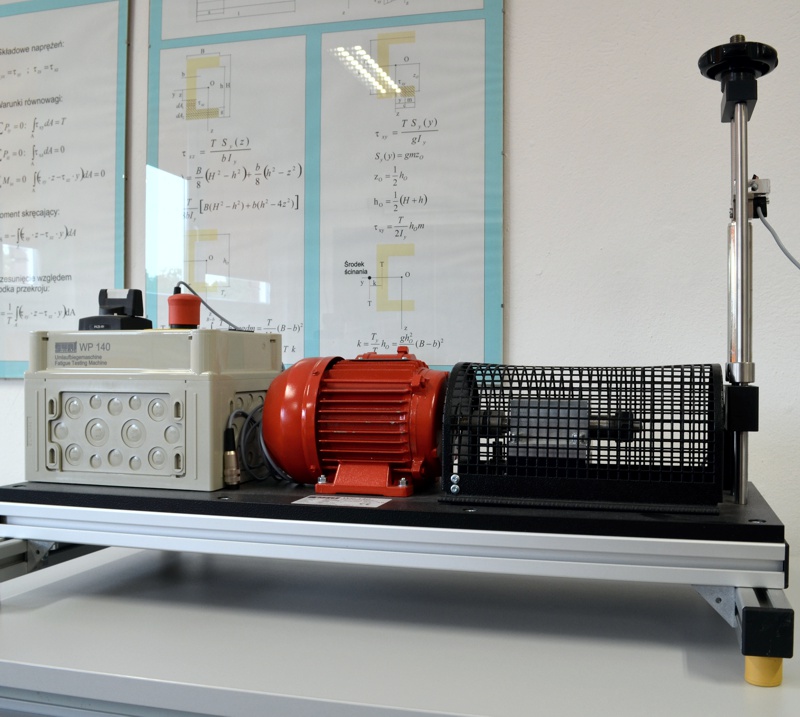
Fatigue Testing Station
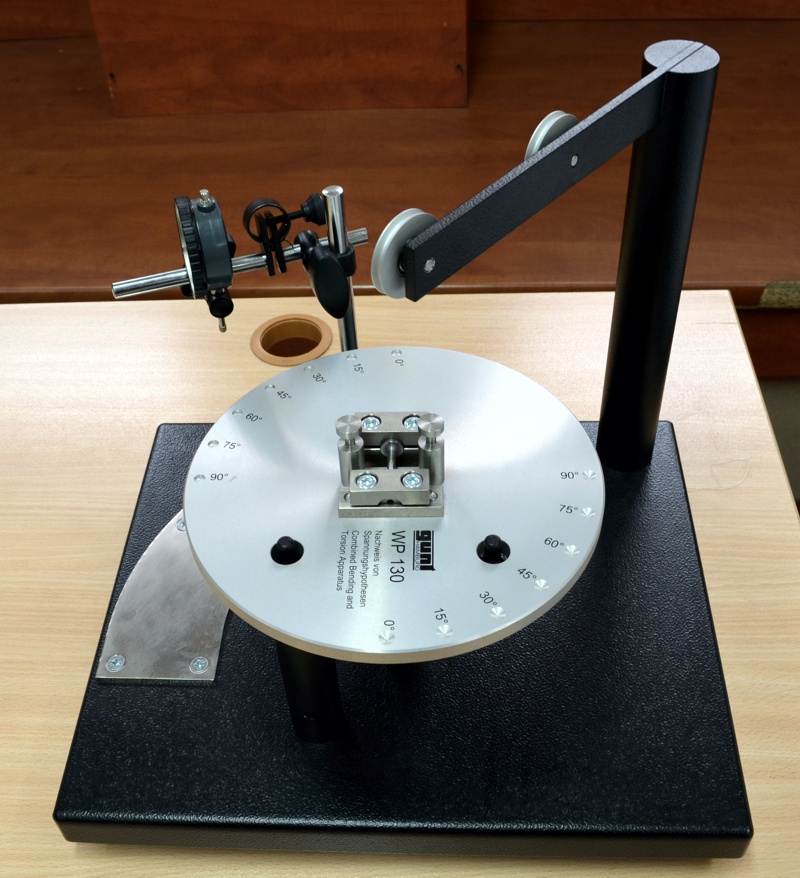
Station for verification of the stress hypotheses
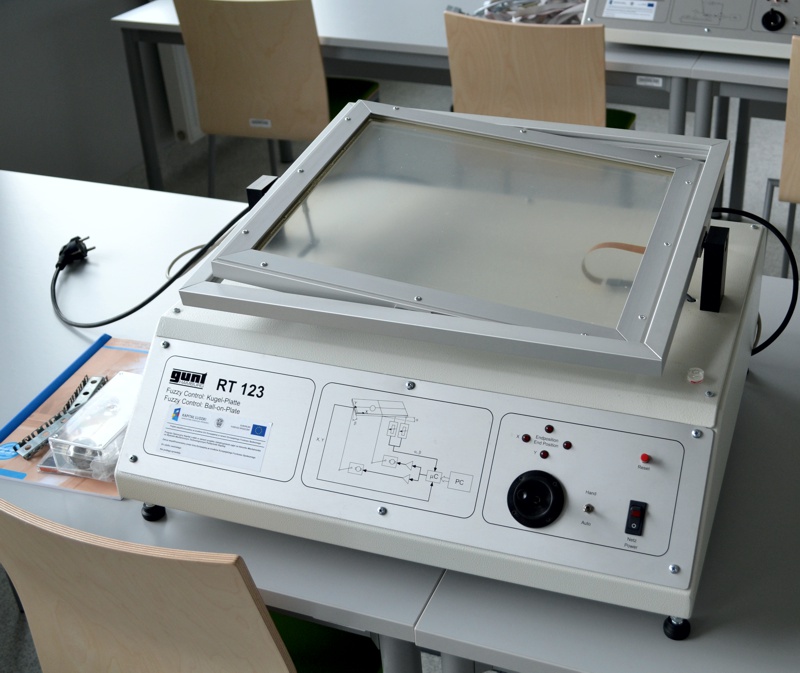
Device with fuzzy control
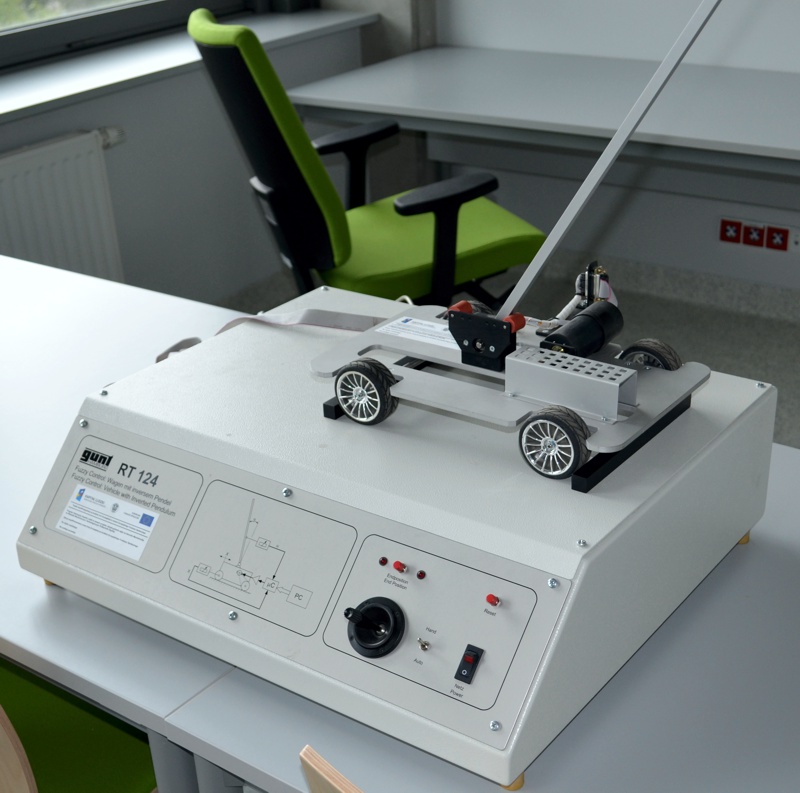
Device with fuzzy control
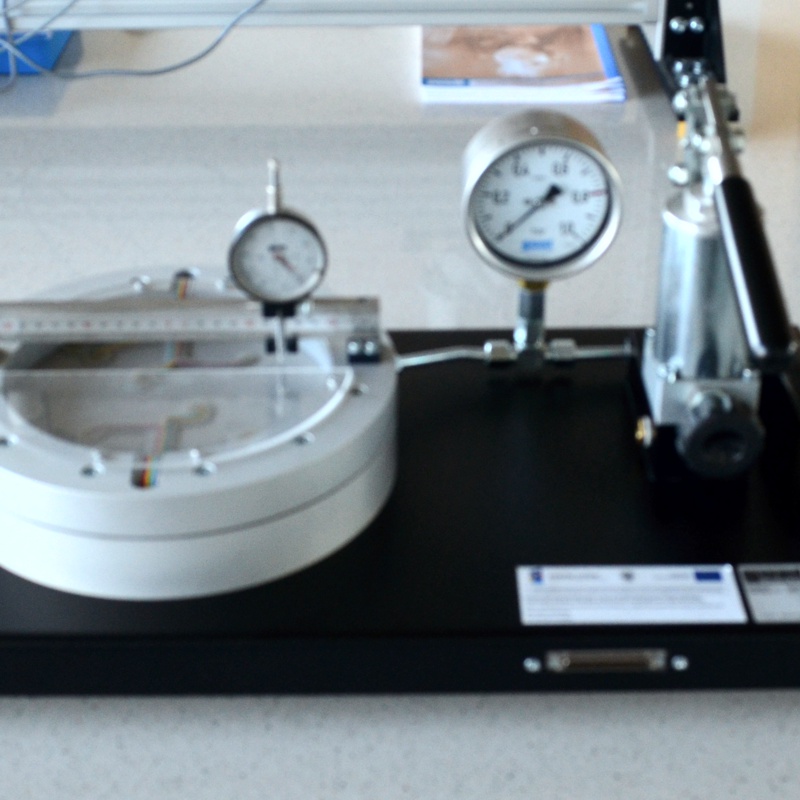
Experimental test station for axisymmetric circular plate
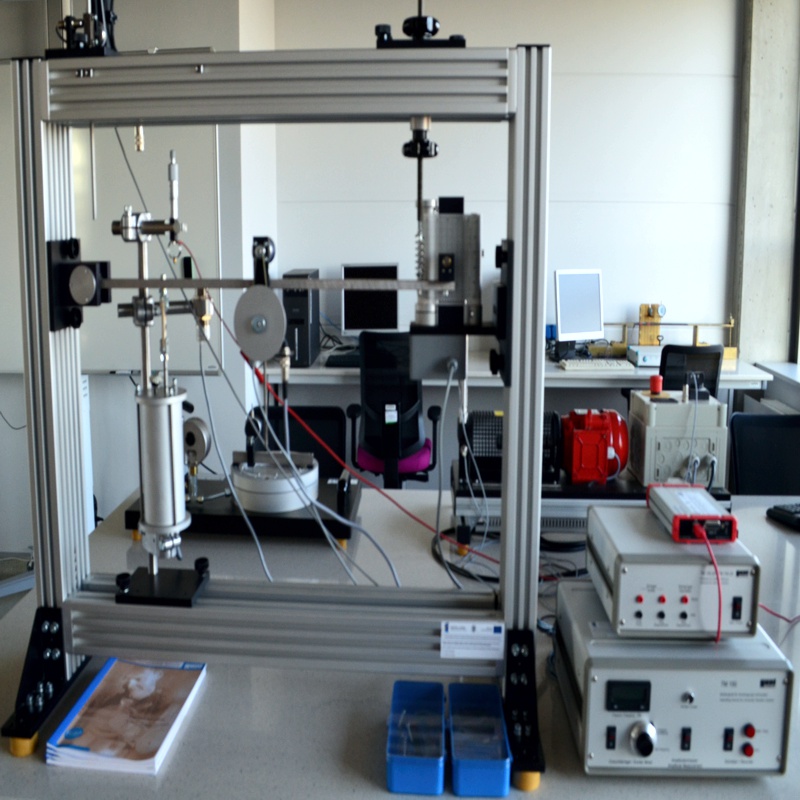
Experimental station for natural vibration
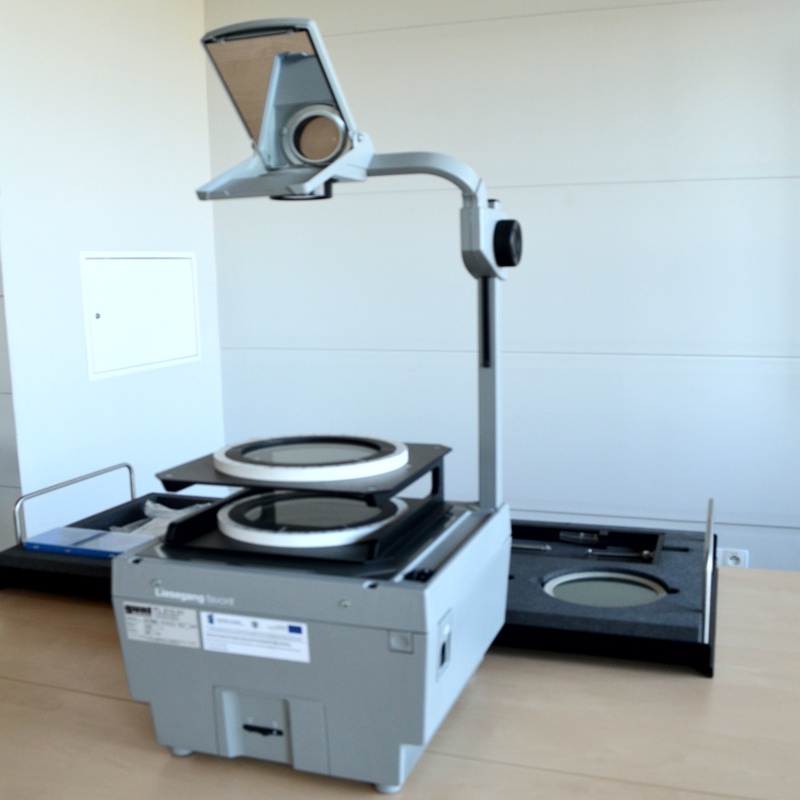
Stress analysis station with elasto-optical method
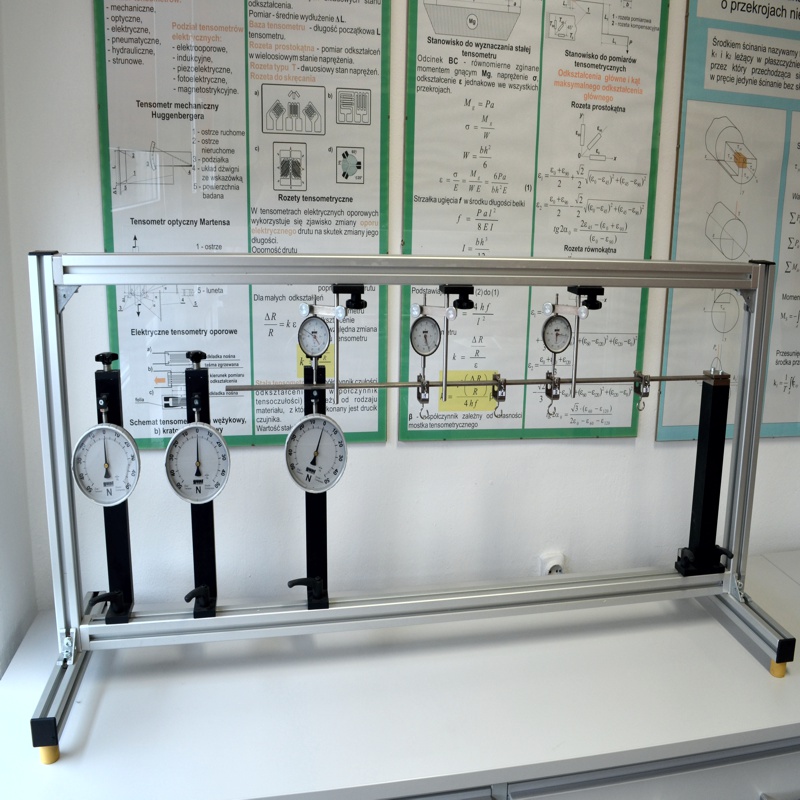
Experimental station for the verification of Betti's and Maxwell's theorems
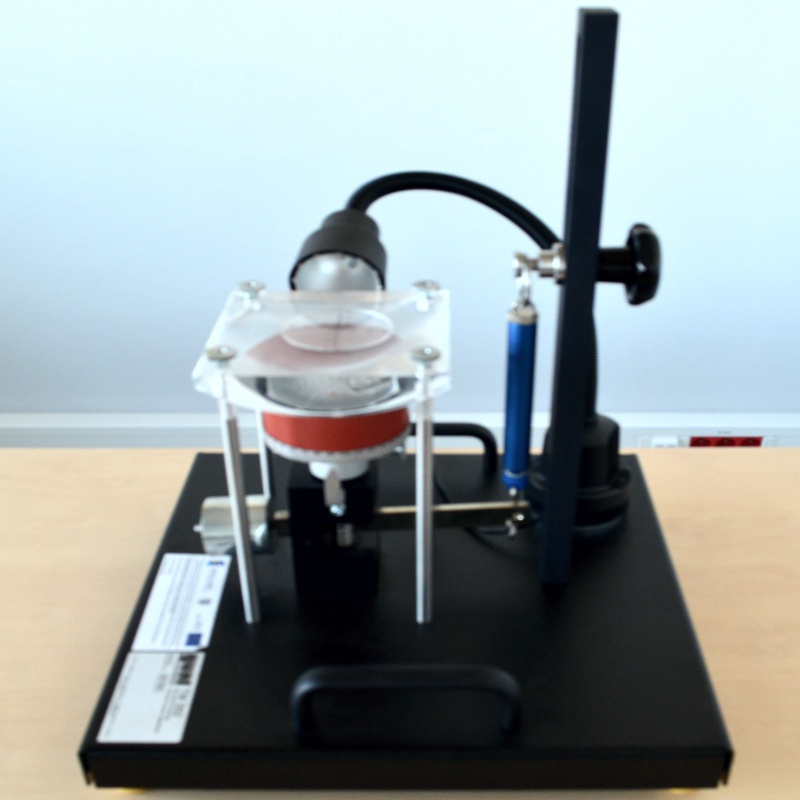
Test station for contact phenomena
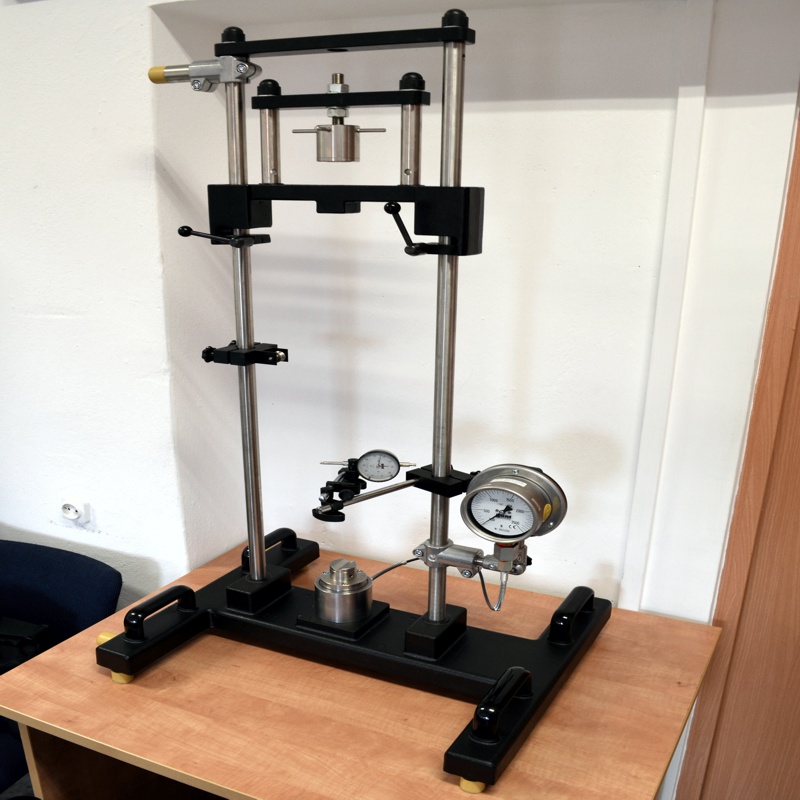
Buckling test station
Knowledge and experience in the field of:
- Thermovision examinations of building insulation
- Thermal diagnostics of electrical and electronic components (including monitoring of power lines and transformers)
- Monitoring of operation of engines, transmissions, turbines, pumps, compressors and generators
- Locating malfunctioning and overheating bearings and bushings
- Checking the operation of valves and other mechanical equipment
- Inspect heat transfer/return lines
- Detection of spontaneous combustion hazards (coal storage, cereals, etc.)
- Thermal control of physical and chemical transformations.
Tests are conducted using modern laboratory equipment.